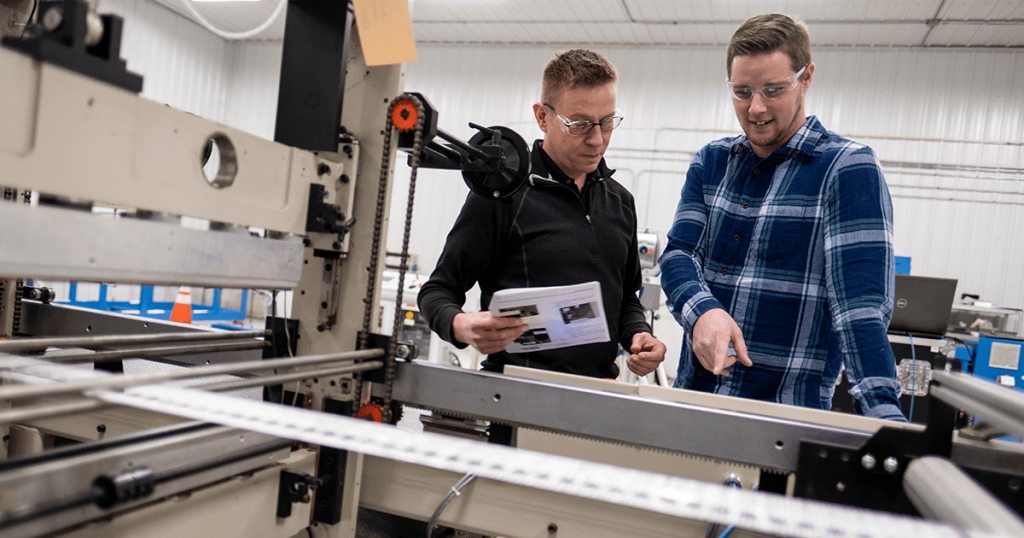
Accurate Testing of Materials, Processes and Equipment Components
As an exclusive service for CMD customers and colleagues, the Advanced Engineering Analytics (AEA) Lab offers real-time testing, future-proofing, innovation-testing and development of pouch and bag styles and products. Operating from a 2,400 sq. ft. facility on the 126,000 sq. ft. CMD campus in Appleton, WI, the AEA Lab utilizes technical experts, established metrics, technology and equipment to analyze data and provide project risk management for CMD customers. Customers can bring raw materials and film with specifications to CMD for technical experts to test, and receive concise, concrete data to apply to their packaging processes.
“Tracking component life and performance using analytical data is extremely important to customers,” says Product Development and Engineering Technician Greg Prellwitz, who oversees the AEA Lab operations. “It provides manufacturers with clear information on when to update parts, change maintenance cycles or create service kits to extend the life of components. With the AEA Lab, CMD is able to project scheduled down time based off performance data from actual run conditions to better utilize up time and maximize performance throughout the service life of components.”
The AEA lab was first introduced as a key strategic initiative and gained momentum in the last two years with the development of the 760-SUP Stand-Up Pouch Machine. The lab has been enlarged, and refined, thanks to the efforts of Prellwitz and Senior Mechanical Engineer Peter Hunnicutt, lab general engineering support. The pouch and bag equipment lab operates within one of the three CMD facilities—a 33,6000 sq. ft. building purchased in 2011. The lab has evolved for the analysis of all CMD machine parts and subsequent products. The spacious, open concept encourages discussion and allows for customer
Key outputs of the lab are:
• Ready access to analytical metrics and technical expertise
• Advanced data analytics for thorough understanding of machine components and the effects on various packaging processes
• Archived reports for easy access to detailed data
The equipment within the AEA Lab allows for detailed analytics of packaging applications such as sealing ability, durability of machine wear parts, component capabilities and strength, materials application, and process validation utilizing a clear, scientific approach.
The lab includes specific equipment targeted to replicate the converting environment, and advanced software to deeply analyze data in real-time. Along with pouch and bag equipment, the lab features a platen test stand for concept testing; evaluation test stand for analyzing equipment reliability; CMD 760-SUP prototype test stand for the testing of component durability; legacy/cross seal test stand providing promising alternatives; and a 760-SUP module tester for process validation.
Other specialized equipment includes a pneumatic seal tester, water bath leak detector, CMD prototype cross sealer and more for the application of various analytics. The Instron Test, Burst Test and high precision measuring are a few of the tests the lab conducts. The AEA Lab also examines how key components, different films and surrounding parts all interact within a process.
Throughout the testing process, CMD archives all data found by the above equipment. These detailed data reports are then easy to attain for futurecustomer application.
Utilizing the AEA Lab, CMD can:
• Vet key processes prior to customer install
• Advise customers on best processes for best quality products
• Offer specific instructions on how to operate, maintain and service CMD equipment
• Install preventive maintenance alerts for scheduled downtime
• Predict failures early for quick remediation
• Test component durability
• Test raw material, film and machine process compatibility
• Accelerate product development
• Provide project risk management
Minimizing Risks for Customers
To succeed in a growing and crowded market like stand-up pouches, customers need new product features and concepts. They need something to make consumers pause and take notice—a “wow” factor, which is often attained by creating a more convenient user experience, such as with microwave and heat-ability, single-serving containers, reclose-ability and, of course, sustainability.
With the AEA Lab’s data tracking, statistical analytics, clear and concise documentation and verified results, customers can test new product designs and decisively validate performance ability. This reduces customer uncertainty and leads to decreased project risk management. It can also accelerate the project time line ahead of competition with the testing of designs prior to finalization, reducing the commercialization process for a competitive advantage.
“For the development of new materials, machineability testing on real-life production processes, the collection of performance data and the ability to analyze the data to confirm success is a real advantage for customers,” says CMD Product Line Manager for Pouch and Intermittent Bag Equipment, Scott Fuller.
Future-Proofing Today
As technology and situations constantly change, knowing production processes and components are secure in their performance capabilities is critical to success in the marketplace. Manufacturers need a guarantee against the future, and this is the purpose behind the design of the AEA Lab.
The AEA Lab provides deeper insights regarding the wear-life of consumables components and product quality verification, tests new and more efficient cost and energy reduction techniques and uses current technology to mitigate potential obsolescence. The CMD AEA Lab is designed to provide future-proofing production techniques and equipment to CMD customers for their manufacturing security. Through the in-depth analytics the lab provides, CMD designs equipment that is slow to obsolete and thoroughly understood by CMD engineers and technicians. These technicians are then able to detect minute changes in performance and provide verified solutions as well as anticipative data for preventive maintenance and scheduled downtime.
This commitment is evidenced by CMD’s new 760-SUP Stand-Up Pouch machine, of which the bag and pouch equipment lab was crucial in developing. The lab provided CMD technicians with in-depth data collection and analytic knowledge regarding viability of design, performance, durability, etc. regarding all machine operations and components, including the components central to the CMD Intelligent Sealing process, a key attribute to the 760-SUP. The success of the 760-SUP prompted CMD to open the lab to all customers and collaborative efforts.
CMD’s Collaboration
Since the creation of CMD in 1980, the firm has worked with materials suppliers up and down the value chain within the flexible packaging and polyethylene film and bag industry. Within the AEA Lab specifically, collaborators such as Exlar, Bosch, Aurora, Flex4, Tolomatic, SKF and more—who have contributed technical knowledge as well as physical components, like linear actuators, load cells, pneumatic cylinders, control platforms, etc.—have made future collaborative efforts through the lab possible.
Such efforts include training exercises, design concepts, software analysis, the microscopic testing of material and components, and the support of CMD service personnel in the field.
“By facilitating these more comprehensive and broader joint ventures with reliable equipment, materials and service providers as well as customers, all involved can grow their knowledge base and understanding of material capabilities and CMD components,” says Senior Mechanical Engineer, Peter Hunnicutt. “This yields more in-depth insights and quicker results for current and future applications.”
Leave a Reply
You must be logged in to post a comment.