The Role of Seal Integrity in a Stable Pouch Converting Process
Share
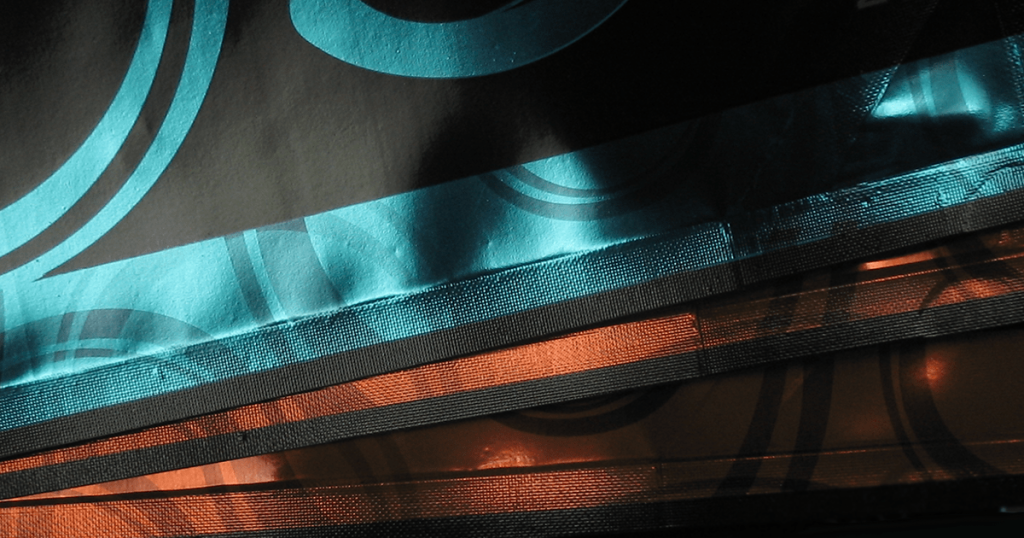
Condensed from presentation by Scott Fuller, CMD Intermittent-Motion Product Line Manager, and Non-Medical Pouch Sales Manager for the U.S. at the inaugural AMI Plastic Pouches conference in Vienna, Austria.
Consistency
In Package Converting, success is achieved through consistency for every pouch, in every lot. Consistency in the ability to provide pouches that perform as specified…every time. Consistently reliable pouches build end-user confidence, enhance brand value, and contribute to repeat customers and repeat sales for converters.
To the individual Consumer, a failed seal is inconvenient. It is time-consuming to clean the mess. It is a relatively low monetary loss. The greater loss is reduced confidence in the product and possibly the brand itself. A failed seal creates doubt – is the product safe? Has it been tampered with? Can I trust it in the future?
To the Brand Owner, a failed seal starts to get costly. Seal
failure in the retort chamber could contaminate the whole batch.
Seal failure in transport could result in rejection of a pallet, or even a full truckload. In extreme cases, product spoilage or contamination due to seal failure could result in product recalls. Even if the failure doesn’t make it to the consumer, loss of confidence in a product at the store level can become very costly to the brand owner.
To the Converter, significant money has been invested to produce a pouch, including $2MM – $3MM USD for a 3-layer extruder ($5MM to $6MM USD for 7-layer); $2.5MM – $3MM USD for a 10-color press; and $1.5 MM USD for a laminator. By the time the material reaches the pouch machine, it is the most it expensive it can be. It is critical that the pouch machine perform consistently and efficiently. Yet, many converters gamble on a pouch-making process that is neither consistent nor efficient. Some lose. That loss can be devastating, even resulting in bankruptcy.
The expectation is that a finished pouch will perform as specified. Is there science to support that expectation?
• “The pouches have always performed well in the past.”
• “That’s why we test and inspect.”
• “We plan for a certain percentage of failures in the market.”
Scientific technology is now available to pouch converters which can provide a confidence that is fact-based, supported by data, and driven by the process.
Temperature, Time and Pressure remain the key ingredients to creating a seal. Reliable control over temperature can be readily achieved. Temperature control in fusion-sealing has, historically, had the most profound impact on seal quality. However, film structures have become increasingly more complex. Time and pressure play a more important roll. Converters are now shifting their focus from simply ‘dialing-in’ the temps, to closely monitoring the effects of time and pressure. Seemingly insignificant system differences combine to produce a significant force differential. Variability in gauges, regulators and air-cylinder condition; spring force and mechanical tolerances requiring frequent “operator tweaks” point to an inherently unstable sealing process.
The Solution
CMD has developed a solution that combines mechanical simplicity with advanced, closed-loop controls technology to provide a sealing process that minimizes variation, and provides access to real-time data to be used for process validation. From a mechanical standpoint, CMD’s Intelligent Sealing Technology eliminates lost motion, minimizes mechanical linkages, and is designed for structural integrity under the most demanding conditions. Advanced controls offer precise, closed-loop force control; real-time process data output for time, temperature, and pressure–each time the sealer makes contact with the substrate.
Intelligent Sealing Technology offers achievable consistency and control. Simplified mechanics, like a fixed anvil design, can minimize sources of variation. Sophisticated, recipe-based controls take much of the process out of the hands of the operator, providing lot-to-lot consistency, regardless of which operator ran the product. Closed-loop feedback, coupled with newer controls applications, provide a more consistent sealing process from pouch-to-pouch and lot-to-lot.By adopting the philosophy of improving and controlling the sealing process, converters better protect the investment of expensive substrates. A verifiable process enhances the converter’s reputation and builds confidence from brand owner through end user.
Leave a Reply
You must be logged in to post a comment.